In the textile industry, different auxiliary chemicals are used according to the performance of various fibers in the various processing processes from spinning, yarn spinning, weaving, printing and dyeing to finished products, in order to improve the quality of textiles, improve the processing effect, increase production efficiency, simplify the process, reduce production costs and give textiles various excellent application properties. Such auxiliary chemicals are commonly known as textile dyeing and finishing auxiliaries. Dyeing and finishing auxiliaries are often divided into three categories according to the steps and uses of dyeing and finishing process: pretreatment agents, printing and dyeing auxiliaries, and finishing agents.
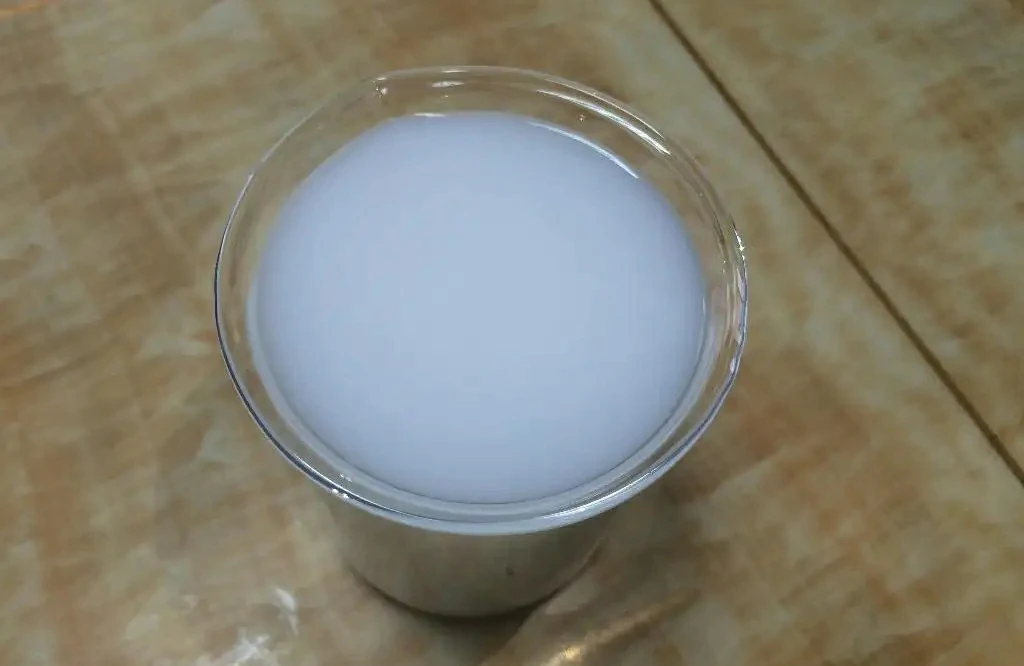
I. Pre-treatment agent for printing and dyeing
The pre-treatment process of printing and dyeing includes fiber burning, desizing, cooking, bleaching, mercerizing and other processing, which requires the addition of penetrants, emulsifiers, cleaning agents and other surfactants, mainly organic sulfates, sulfonates and polyoxyethylene ethers.
1. Penetrant, wetting agent textile industry commonly used penetrant ricinoleic acid butyl ester of sulfate, butyl naphthalene sulfonic acid sodium salt, etc.. In neutral solutions, dioctyl succinate sulfate sodium permeability is particularly strong; in acidic solutions in addition to the above species, commonly used fatty alcohol polyoxyethylene ether or alkyl phenol polyoxyethylene ether; and in strong alkaline solutions, such as mercerization process to use shorter carbon chain sulfate ester such as octyl sulfate.
2. Emulsifier in the textile process as to improve the lubricating properties of silk and yarn, often to oil. But before the printing and dyeing process to remove the oil, so as not to affect the dyeing, so in these textile oil agent to add emulsifier beforehand, or in the cleaning bath to add emulsifier to ensure the removal of oil spots, generally with non-ionic surfactants.
3. Cleaning agents, that is, detergents, net detergents to remove oil and grease on textile articles, in the past, mainly soap, but now a variety of synthetic detergents and non-ionic surfactants, and including slightly more expensive oleic acid amide derivatives.
In addition, there are enzymes used to promote starch hydrolysis during desizing; activators and anti-corrosion agents added during bleaching to speed up the bleaching process and increase whiteness without corroding equipment. At present, has developed to desizing, cooking, bleaching a bath to complete, and the use of a new compound of powerful cleaning additives.
Second, printing and dyeing auxiliaries
The varieties of textile dyestuff are relatively large, the dyeing process is different, the corresponding supporting auxiliaries required, so there are a wide variety of such auxiliaries, mainly the following.
1. Water softener: that is, metal ion chelator heavy metal ions in water often affect the color of dyes or their dissolution properties, we can use water softeners to remedy the common varieties of water softeners are sodium hexametaphosphate, sodium ammonia triacetate and sodium ethylenediaminetetraacetic acid, etc.
2. solvent and co-solvent certain dyes in the use or preparation of liquid dyes, need to fill force mouth solvent to help its dissolution, such as ethylene glycol, a diethylene glycol, glycol ether, formamide, thiobisethanol, etc. can be used as a dye solvent; with phthalo blue dyeing, to use the supporting co-solvent and copper salt, reduction dyes with co-solvent benzylaminobenzene sulfonic acid sodium.
3. reducing agent and oxidizing agent reducing dyestuff in use must first use reducing agent to dissolve reducing dyestuff, commonly used are insurance powder (even sodium bisulfite), hanging white block (formaldehyde sodium bisulfate), thiourea dioxide. Reduction of dyestuff to prevent dyeing available light oxidant sodium m-nitrobenzene sulfonate, this product can also be used for printing paste, in order to protect the dyestuff from the possible reduction of components in the paste with the impact.
4. color fixing agent and color development auxiliaries with direct dyes, acid dyes and reactive dyes dyeing, before and after dyeing with color fixing agent treatment, can improve the amount of color and fastness. Color fixing agent is mainly used amine salt and polymer quaternary ammonium salt. Dyestuffs for printing sometimes use color development aids, such as fast amine steam color development with diethyl ethanolamine.
5. Dispersants, also known as diffusers with disperse dyes and reduction dyes when printing and dyeing to add dispersant and protective colloid to ensure uniform dyeing and prevent color spots. Commonly used dispersants are sulfonated oil (Swire oil, Turkish oil), alkyl or long-chain amide-based benzene sulfonic acid sodium, alkyl polyoxyethylene ether, sodium lignin sulfonate, naphthalene sulfonic acid formaldehyde condensate, oleoyl polyamine carboxylate, etc.
6. leveling agent, that is, even dyeing agent dyestuff commonly used polyoxyethylene ether surfactants as leveling agent, cationic dyestuff to use cationic surfactants, acid dyestuff to use anionic surfactants.
7. matting agent compared with natural fibers, synthetic fiber surface is too smooth, reflectivity is too high, so must add titanium dioxide, zinc sulfide, etc. to improve.
8. Defoamer for the printing and dyeing process to remove surfactant-induced foaming. The original general use of tributyl phosphate, octanol, etc., now have been used in the organic stone-grey compound.
9. printing pulp and thickeners used to use natural pulp, now has tended to use semi-synthetic or synthetic pulp, such as starch ether, sodium alginate, etherized acacia bean powder, cellulose ester, polyvinyl alcohol and polyacrylate, etc.. Synthetic slurry consistency is high, the amount of less, can make the printing of the resulting color deep. The chemical structure of the thickener is polymer polyethylene glycol double ether or double ester or polyacrylate copolymerized by acrylate, etc.
10. Adhesives for printing and dyeing can be used in various synthetic latexes such as butadiene, styrene, acrylonitrile, vinyl acetate, vinyl chloride and acrylate copolymers. Require strong adhesion that is good abrasion resistance, feel soft, at high temperatures and in the light is not easy to yellow. At present, the higher quality of general-purpose adhesives with self-crosslinking groups of polyacrylate copolymers and polyurethane class.
Three, printing and dyeing after finishing cleaning agent
After the completion of the printing and dyeing process, the fabric should generally be cleaned to remove the floating color to improve dyeing fastness, the synthetic cleaning agent used with the dyestuff and printing and dyeing processing methods vary, such as disperse dyestuff dyeing polyester and cotton fabrics, both to remove the floating color on polyester, but also to prevent put dirt cotton fiber part, must use a special non-ionic cleaning agent.
1. Finishing agent is used to improve the appearance of fabrics, feel, shrinkage, stabilize the shape, extend the life, waterproof, fire, stain, mildew and other chemicals used. Resin finishing agent, the most important finishing agent, is a polymer compound, and cellulose hydroxyl bonding, so as to achieve a more durable wrinkle-free effect. Mixed with the appropriate softener, can improve the feel of the fabric. Commonly used resins are urea-formaldehyde resin, melamine formaldehyde resin, di-hydroxymethyl vinyl urea resin, di-hydroxymethyl di-hydroxy vinyl urea resin and di-hydroxyethyl sulfone, etc.. Among them, the most common application of dihydroxymethyl dihydroxyvinyl urea resin is condensed with glyoxal, urea and formaldehyde. In the resin finishing working solution to add penetrant, catalyst [commonly used metal salts, ammonium salts or organic amine salts) and feel adjuster, the latter is usually a softener. The newly developed resin finishing agent, polyurethane, is slightly more expensive, but has high setting performance, no residual formaldehyde, and does not cause skin allergy problems.
2. Softener is mainly cationic long-chain fatty finishing agent, due to cationic finishing agent has an affinity for fibers, the amount can be reduced, and strong adhesion, can show a more durable softness, its soft lubricating properties mainly from its long-chain fatty base. In this softener with emulsified mineral oil, wax can increase the lubricity. Some softeners react with the hydroxyl or amine group in the fiber, so that the fiber’s washability is enhanced and has long-lasting softness. Recently, the emergence of silicone oil dispersion softener, its ionicity varies according to the emulsifier used, the fabric has a particularly soft and smooth feeling after treatment, suitable for high-speed sewing. Such as the addition of cross-linked silicone compounds, but also to enhance the elasticity of the fabric.
3. Waterproof agent rubber pulp coating can be waterproof, but poor breathability when wearing. Rainproof paste is a mixture of aluminum salts and paraffin, but not durable. Durable waterproofing agent with breathability, to use the long-chain aliphatic hydrocarbon compounds that react with the fabric.
Acrylate coatings can also be waterproof after cross-linking, and newly developed waterproofing agents are hydrogen-containing silicone oils and their derivatives.
4. flame retardants temporary flame retardants are amine salts, sodium tungstate, borax, water glass, etc. Diammonium hydrogen phosphate and urea together with the treatment of cotton cloth, can have a certain durability. Organic substances are mainly compounds containing bromine, phosphorus, nitrogen and chlorine, which can inhibit combustion. If it can be combined with fiber, it can play a lasting role.
The main varieties of flame retardants for cotton, with the following structure: for synthetic fibers there is still a lack of effective durable flame retardants, polyester had used tris (2,3-dibromopropyl) phosphate, flame retardant effective, but because of its toxic, has been banned in 1977. Now use is tetrahydroxy phosphorus chloride compounds, sulfides or hydroxyl compounds and resins, durability is better. There are also flame retardants added before the spinning of synthetic fibers, but there is a certain impact on fiber performance and strength. Currently, new polybromides are being developed as flame retardants for synthetic fibers.
5. Static prevention agent, that is, antistatic agent is mainly used for synthetic fibers, both to prevent the generation of static electricity, but also to make the fabric easy to decontaminate. There are mainly polyacrylic acid, polyethylene glycol ester and polymer amphoteric compounds.
6. Anti-mildew additives cotton fabrics in the presence of microorganisms, prone to mildew, especially in the presence of pulp and the appropriate temperature and humidity conditions, more prone to mildew, the application of anti-mildew agents are a variety of copper salts, and organic phenol derivatives, such as copper pentachlorophenol, copper naphthenate, copper 8-hydroxyquinoline and dihydroxy dichlorodiphenylmethane, salicylanilide, etc..
7. Oil repellents are mainly various derivatives of organic fluorine, which have a particularly low surface energy, do not stain oil, and are bonded to fibers in a resin-like structure.
8. coating agent is a new finishing agent, polyacrylate, polyurethane, etc., they give the fabric a variety of additional properties, such as waterproof, flame retardant, light, elastic, so that inexpensive fabrics have a class such as leather performance.
9. Functional finishing agents and many other finishing agents that give fibers special functions, such as far-infrared warming and health finishing agents, anti-UV emulsion treatment agents, antibacterial health finishing agents, ceramic powder far-infrared finishing agents, aromatic finishing agents, etc.
*Disclaimer: The content contained in this article comes from the Internet, WeChat public numbers and other public channels, and we maintain a neutral attitude toward the views expressed in the article. This article is for reference and exchange only. The copyright of the reproduced manuscript belongs to the original author and the institution, and if there is any infringementPlease contact Jetson Chemical for deletion