在浮选过程中,有时为了提高药剂(例如捕收剂)的分散和浮选效果,需先加乳化剂,对药剂加以乳化处理;有的选矿药剂本身易于乳化,而矿浆中的乳化泡沫会影响后步工序,造成精矿溢流损失或尾矿废水对河川的污染。
为此,在上述情况下需添加破乳剂加以处理。使用破乳剂时需先调整乳浊液的pH值,对于强碱、强酸乳浊液一般需将pH值调至1~10的范围。在石油、化工、毛纺和机械加工等行业的含油乳浊液的废水处理中,除了用物理破乳方法(如加热法、膜分离法、电场破乳法)以外,也常用破乳剂进行化学处理。普遍使用的破乳剂是由多种组分构成的高分散性的混合物。对水包油型乳浊液的破乳通常用带有H+、Al3+、Fe3+等阳离子的无机物作破乳剂,如无机酸、硫酸铁等;而对油包水型乳浊液的破乳,一般用阴离子型和非离子型表面活性剂或两者的混合物作为破乳剂。
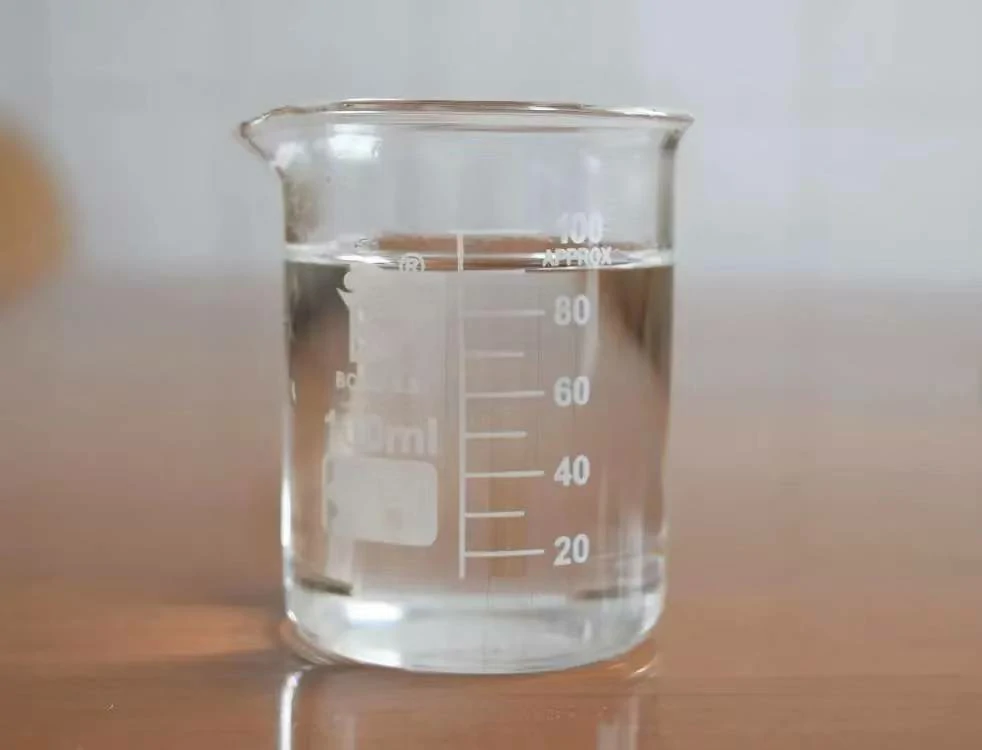
由于一些固体难溶于水,当这些固体一种或几种大量存在于水溶液中,在水力或者外在动力的搅动下,这些固体可以以乳化的状态存在于水中,形成乳浊液。理论上讲这种体系是不稳定的,但如果存在一些表面活性剂(土壤颗粒等)的情况下,使得乳化状态很严重,甚至两相难于分离,典型的是在油水分离中的油水混合物以及在污水处理中的水油混合物,在此两相中形成比较稳定的油包水或者水包油结构,其理论基础是“双电层结构”。
在此情况下,投入一些药剂,以破坏稳定的双电层结构,以及稳定乳化体系,从而达到两相分离的目的。使用的这些为了达到破坏乳化作用的药剂称之为破乳剂。
破乳机理
由于油、油层水及所含天然乳化剂组成的复杂性,对油水界面上发生的物理化学过程的研究又极其困难,因而对化学破乳剂的破乳过程和破乳机理仍处于研究之中,但破乳剂和乳化剂都是表面活性物质,两者的作用却截然相反。现将各种破乳剂的破乳机理归纳如下:
表面活性作用。破乳剂都具有高效能的表面活性物质,破乳剂较乳化剂有更高的活性,有文献认为破乳剂活性应比乳化剂大100~1000倍,使破乳剂能迅速地穿过乳状液外相分散到油水界面上,替换或中和乳化剂,降低乳化水滴的界面张力和界面膜强度,使形成W/O型乳状液变得很不稳定。界面膜在外力作用下极易破裂,从而使乳状液微粒内相的水突破界面膜进入外相,从而使油水分离。这不仅可以破坏已经形成的原油乳状液,还可以防止油水混合物进一步乳化,起到降低油水混合物黏度和加速油水分离的作用。但实践表明,不存在破乳剂活性越高,破乳能力越强的规律。
反相乳化作用。原油乳状液是在原油中憎水的乳化剂作用下形成的,俗称W/O型乳状液,如环烷酸、沥青质等。采用亲水型的破乳剂可以将乳状液转化为O/W型乳状液,借乳化过程的转换以及O/W型乳状液的不稳定性而使油水分离。当破乳剂促使油包水转相形成水包油型乳状液时,此时水在外面很容易碰撞聚集成大水滴沉降出来。
“润湿”和“渗透”作用。破乳剂可以溶解吸附在油水界面的胶质、沥青质、固体粉末等天然乳化剂,防止天然乳化剂构成的界面膜阻碍水滴聚结。如黏土、硫化铁、钻井泥浆等固体颗粒具有亲水性,破乳剂能把这些固体乳化剂从油水界面拉入水滴内;沥青质和高熔点蜡晶等具有亲油性,破乳剂能让其离开油水界面进入原油内。这样,有利于水滴碰撞时的合并,达到水滴下沉的目的。
由于原油乳状液中呈分散相的水滴总是带负电荷,并在自己的表面上吸附了一部分正离子,使分散相往往带有正电,因为所带电荷相同,分散相的水滴之间互相排斥,水滴难于合并。如果在原油中加入离子型的破乳剂,极性相反的离子被吸附在水滴表面并将正电荷中和,使水滴的静电斥力减弱,破坏受同性电保护的界面膜,使水滴合并从油中沉降下来。
尽管破乳剂的破乳机理尚不完善,但从长期实践中归纳出两点结论:①破乳剂的分子量大于天然乳化剂的分子量才能有效破乳;②若把破乳剂用作油水混合物的乳化剂,则生成反相乳状液,即O/W型乳状液。
主要用途
破乳剂是一种表面活性物质,它能使乳化状的液体结构破坏,以达到乳化液中各相分离开来的目的。原油破乳是指利用破乳剂的化学作用将乳化状的油水混合液中油和水分离开来,使之达到原油脱水的目的,以保证原油外输含水标准。
破乳剂分类
按照目前破乳剂使用的情况,可将破乳剂分为水溶性破乳剂和油溶性破乳剂两大类。
破乳剂属表面活性剂类型,破乳剂分子由亲油、亲水基团组成,亲油部分为碳氢基团,特别是长链碳氢基团构成;而亲水部分则由离子或非离子型的亲水基所构成。破乳剂的种类繁多,若按表面活性剂的分类方法可分为:阳离子型、阴离子型、非离子型、两型离子型破乳剂。
阴离子破乳剂溶于水后生成的亲水基团为带负电荷的离子团,按其亲水基又分为:羧酸类、磺酸类、硫酸酯类和磷酸酯类。阴离子型破乳剂有羧酸盐类、磺酸盐类和聚氧乙烯脂肪硫酸酯盐等,具有用量大、效果差、易受电解质影响而减效等缺点。
阳离子破乳剂溶于水后生成的亲水基团为带正电荷的粒子团,亲水基主要为碱性氮原子,也有磷、硫、碘等。阳离子型破乳剂主要有季铵盐类,其对一般原油有明显效果,但不适合稠油及老化油。
非离子破乳剂溶于水后不离解离子,因而不带电荷。非离子型主要有以胺类为起始剂的嵌段聚醚,以醇类为起始剂的嵌段聚醚,烷基酚醛树脂嵌段聚醚,酚胺醛树脂嵌段聚醚,含硅破乳剂,超高相对分子质量破乳剂,聚磷酸酯,嵌段聚醚的改性产物以及以咪唑啉原油破乳剂为代表的两性离子型破乳剂。
两型破乳剂为溶于水后可生成正、负两种离子。它在酸性溶液中呈阳离子型,在碱性溶液中呈阴离子型。
油田中常用的非离子型破乳剂主要有以下几种:
1.SP型破乳剂
SP型破乳剂的主要组分为聚氧乙烯聚氧丙烯十八醇醚,理论结构式为R(PO)x(EO)y(PO)zH,式中:EO-聚氧乙烯;PO-聚氧丙烯;R-脂肪醇;x、y、z-聚合度。SP型破乳剂外观呈淡黄色膏状物质,HLB值为10~12,溶于水。SP型非离子型破乳剂对石蜡基原油具有较好的破乳效果。其疏水部分由碳12~18烃链组成,其亲水基是通过分子中的羟基(-OH)、醚基(-O-)与水作用形成氢键而达到亲水的目的。
由于羟基、醚基亲水性较弱,所以只靠一两个羟基或醚基不能把碳12~18烃链疏水基拉入水中,必须有多个这样的亲水基,才能达到水溶的目的。非离子型破乳剂的分子量越大,分子链越长,所含的羟基和醚基越多,它的拉力越大,对原油乳状液的破乳能力越强。SP型破乳剂适应于石蜡基原油的另一个原因是石蜡基原油不含或极少含胶质和沥青质,亲油性表面活性剂物质较少,相对密度较小。对含胶质和沥青质较高(或含水大于20%)的原油,SP型破乳剂的破乳能力较弱,原因是分子结构单一,无支链结构和芳香结构。
2.AP型破乳剂
AP型破乳剂是以多乙烯多胺为引发剂的聚氧乙烯聚氧丙烯聚醚,是一种多枝型的非离子型表面活性剂,分子结构式为:D(PO)x(EO)y(PO)z H,式中:EO-聚氧乙烯;PO-聚氧丙烯;R-脂肪醇;D-多乙烯多胺:x、y、z-聚合度。
AP型结构的破乳剂用于石蜡基原油乳状液的破乳,效果好于SP型破乳剂,它更适合于原油含水率高于20%的原油破乳,并能在低温条件下达到快速破乳的效果。如SP型破乳剂在55~60℃、2h内沉降破乳的话,AP型破乳剂只需在45~50℃、1.5h内沉降破乳。这是由于AP型破乳剂分子的结构特点所致。引发剂多乙烯多胺决定了分子的结构形式:分子链长且支链多,亲水能力高于分子结构单一的SP型破乳剂。多支链的特点决定了AP型破乳剂具有较高的润湿性能和渗透性能,当原油乳状液破乳时,AP型破乳剂的分子能迅速的渗透到油水界面膜上,比SP型破乳剂分子的直立式单分子膜排列占有更多的表面积,因而用量少,破乳效果明显。目前该类破乳剂是大庆油田使用较好的非离子型破乳剂。
3.AE型破乳剂
AE型破乳剂是以多乙烯多胺为引发剂的聚氧乙烯聚氧丙烯聚醚,是一种多枝型的非离子型表面活性剂。与AP型破乳剂相比,所不同的是AE型破乳剂是一种二段型的聚合物,其分子小,支链短。分子结构式为:D(PO)x(EO)yH,式中:EO-聚氧乙烯:PO-聚氧丙烯:D-多乙烯多胺;x、y -聚合度。虽然AE型破乳剂和AP型破乳剂的分子相貌存在很大的差异,但分子成分是相同的,只是在单体用量和聚合顺序上有所差别。
两种非离子型破乳剂在设计合成时,其头、尾的用料量不同,产生聚合分子的长短也不同。
AP型破乳剂的分子为二段式的,以多乙烯多胺为引发剂,与聚氧乙烯、聚氧丙烯聚合形成嵌段共聚物:AE型破乳剂的分子为二段式的,以多乙烯多胺为引发剂,与聚氧乙烯、聚氧丙烯聚合形成两段共聚物,因此,设计出的AP型破乳剂的分子应比AE型破乳剂的分子长。
AE型是两段多支结构的原油破乳剂,同样适应于沥青质原油乳状液的破乳。沥青基原油中亲油的表面活性剂含量越多,粘滞力越强,油水密度差小,不易破乳。而采用AE型破乳剂破乳速度快,同时,AE型破乳剂又是较好的防蜡降粘剂。由于其分子的多支结构,极易形成微小的网络,使原油中已形成的石蜡单晶落入这些网络,阻碍石蜡单晶体自由运动,不能相互连接,形成石蜡的网状结构,降低原油的粘度和凝固点,防止蜡晶聚结,从而达到防蜡的目的。
4.AR型破乳剂
AR型破乳剂由烷基酚醛树脂(AR树脂)与聚氧乙烯、聚氧丙烯聚和而成的新型油溶性的非离子型破乳剂,HLB值在4~8左右,破乳温度低达35~45℃。分子结构式为:AR(PO)x(EO)y H,式中:EO-聚氧乙烯;PO-聚氧丙烯;AR-树脂;x、y、z-聚合度。AR树脂在合成破乳剂的过程中,既起引发剂的作用,又进入破乳剂的分子中成为亲油基。AR型破乳剂的特点是:分子不大,在原油凝固点高于5℃的情况下有较好的溶解、扩散、渗透效应,促使乳化水滴絮凝、聚结,能在45℃以下,45 min内把含水率在50 %~70 %的原油中的水脱出80 %以上,这是SP型、AP型破乳剂所不能比的。
选择破乳剂的基本原则
破乳剂能使原乳状液稳定的因素消除,从而导致乳状液的聚集、聚结、分层和破乳。乳状液稳定的主要原因是由乳化剂形成带电的(或不带电的)有一定力学强度或空间阻碍作用的界面膜。因此,破乳剂的主要作用是消除乳化剂的有效作用,选择破乳剂要针对乳化剂的特性进行选择。
有良好的表面活性,能将乳状液中的乳化剂从界面上顶替下来。乳化剂都有表面活性,否则不能在界面上形成吸附膜,这种吸附作用是自发过程。因此破乳剂也必须有强烈的界面吸附能力才能顶替乳化剂。
破乳剂在油一水界面上形成的界面膜不可以有牢固性,在外界条件作用下或液滴碰撞时易破裂,从而液滴易发生聚结。
离子型的乳化剂可使液滴带电而稳定,选用带相反电荷的离子型破乳剂可使液滴表面电荷中和。
相对分子质量大的非离子或高分子破乳剂溶解于连续相中,可因桥连作用使液滴聚集,进而聚结、分层和破乳。
固体粉末乳化剂稳定的乳状液可选择固体粉末良好的润湿剂作为破乳剂,以使粉体完全润湿进入水相或油相。
由这些原则可以看出,有的乳化剂和破乳剂常没有明显的界限,需视具体体系而定。当然,也有一些表面活性剂只适用于做某一种乳状液的破乳剂,对其他体系既不能做破乳剂也不能做乳化剂。
*Disclaimer: The content contained in this article comes from the Internet, WeChat public numbers and other public channels, and we maintain a neutral attitude toward the views expressed in the article. This article is for reference and exchange only. The copyright of the reproduced manuscript belongs to the original author and the institution, and if there is any infringementPlease contact Jetson Chemical for deletion